April 2015, Vol. 242, No. 4
Features
Designing, Building Pipeline Infrastructure for CO2 Transport
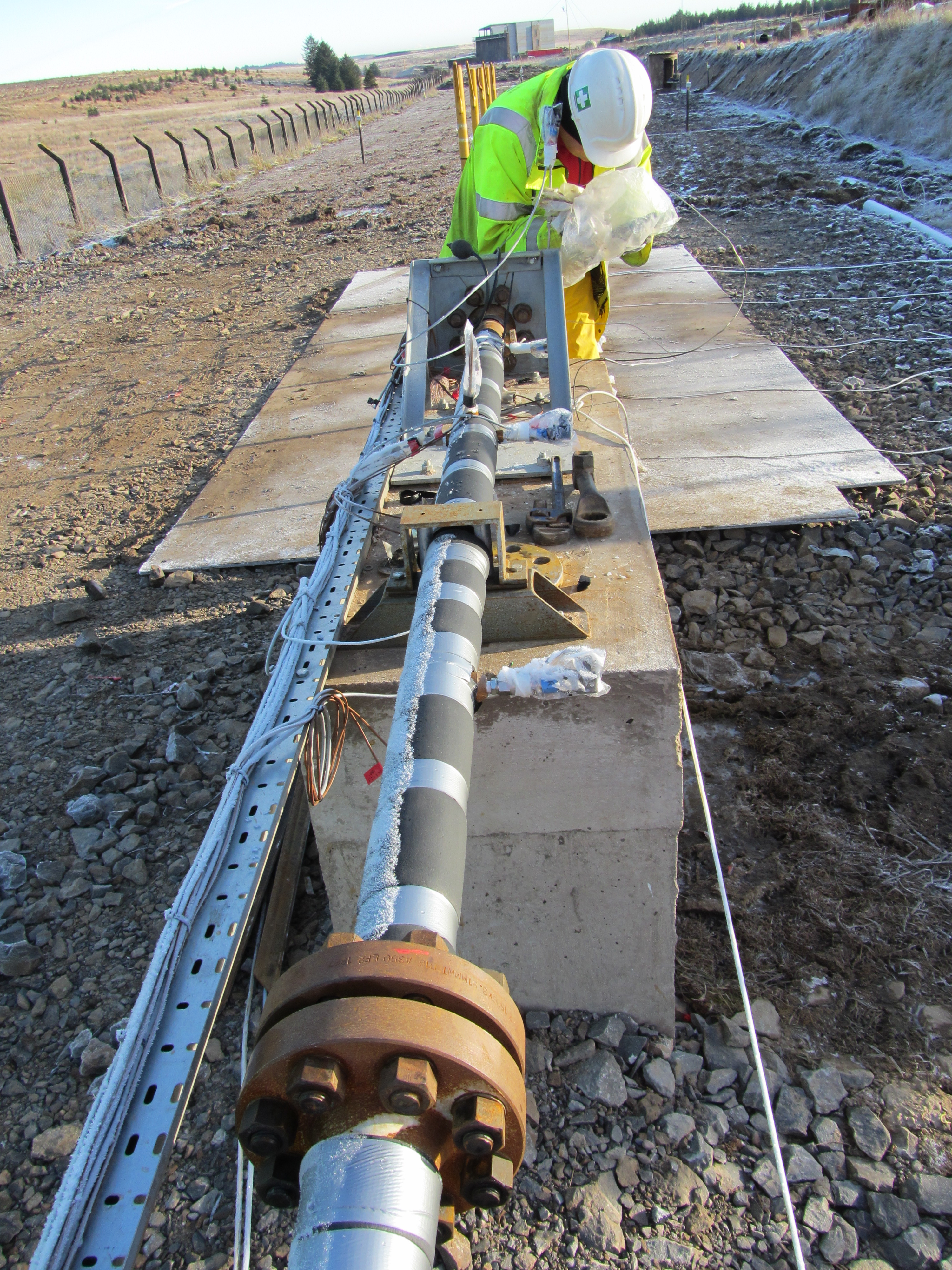
With energy security and climate change at the top of the global agenda, carbon capture utilization and storage (CCUS) is gaining momentum. CCUS technology offers a solution supporting production of incremental hydrocarbon reserves from existing fields while storing CO2 away from the atmosphere.
Transportation of CO2 is generally considered the most uncomplicated part of CCUS since pipelines are a well-known technology. However, closing existing knowledge gaps associated with the safety and reliability of the pipeline transport of CO2 has the potential to reduce uncertainty and avoid unnecessary overdesign of the pipelines.
To address these challenges, the CO2PIPETRANS Joint Industry Project (JIP) was initiated in 2009 by DNV GL. The aim was to produce a guideline for design and operation of CO2 pipelines, based on relevant experience from both the natural gas pipeline sector and the CO2 enhanced oil recovery (EOR) sectors.
To produce the guideline, an in-depth analysis of the main challenges to the design and operation of CO2 pipelines was undertaken. This consisted of seven studies into the main issues that were identified as being different between natural gas pipelines and the current status of knowledge in the field for CO2 pipelines. The topics were fatigue, running ductile fractures, pipeline operation, flow assurance, corrosion, material compatibility and safety issues.
These studies were used to undertake a review and gap analysis for both onshore and offshore CO2 pipelines. The resulting guideline was used as the basis for developing the world’s first recommended practice for design and operation of CO2 pipelines, DNV-RP-J202. Through these studies, gaps in existing knowledge were identified and the basis for designing an experimental program to fill the gaps was formed.
CO2PIPETRANS was then divided into three work packages designed to fill the most crucial knowledge gaps identified, focusing on dense phase CO2 release model validation data, fracture arrest and corrosion. JIP partner organizations participating are: Arcelor Mittal, BP, DNV GL, Endesa, ENI, E.ON Ruhrgas, Gassco, Gassnova, Health and Safety Executive (HSE) UK, Maersk Oil, Petrobras, Petroleum Safety Authority (PSA) Norway, Shell, V&M Tubes and Vattenfall. The sharing of technical knowledge and financial contributions from the partners illustrates the importance the industry itself has put on the issue.
Validation of Modeling
Understanding how CO2 disperses in the atmosphere under both planned and accidental scenarios is an essential element in the route planning and risk-assessment processes of pipeline design. Models are used to simulate what might happen in the case of a release. Until now, these models have not been validated using large-scale experimental results, as experimental data for CO2 has not been publicly available.
The CO2 release model validation data made publicly available through CO2PIPETRANS includes two programs of experiments previously undertaken separately for BP and Shell at the DNV GL (formerly GL Noble Denton) Spadeadam test site in the United Kingdom. The experiments involved the horizontal release of pressurized liquid and supercritical (dense) phase CO2 through ¼-inch, ½-inch and 1-inch (6–25mm) orifice diameters.
In addition to these, two further experimental programs were undertaken. The first program consisted of pipe depressurization experiments, sometimes referred to as shock-tube experiments, which involved the sudden release of 1,450 psi (100 barg) CO2 from one end of a 656-foot-long (200m), 2-inch (50mm) diameter, horizontal pipe through orifice diameters ranging from full-bore down to ?-inch (10mm).
These were performed by filling the pipe to the required test pressure and temperature whereupon a bursting disc at one end was deliberately ruptured. Pressure, temperature and mass instrumentation along the pipe recorded the depressurization with additional data being recorded within the release plume. Video footage was also recorded of the release plume as well as through the pipe at the mid-length location. The pipe was insulated for some of the releases.
The second experimental program involved eight dense phase CO2 experiments at Spadeadam during which dense phase CO2 was released through 1-inch, 2-inch, 4-inch and 6-inch (25-150mm) orifice diameters. The releases were horizontal, at 39 inches (1m) above the ground, with initial pressures ranging between 522 psi and 1,932 psi (36-96 barg) and temperatures between 50°-59° F (10-15° C).
Measurements included pressure and temperature at several locations in the supply reservoir, feed lines and discharge pipe, while direct flow rate measurements were carried out for the 1-inch (25mm) releases only. In addition, field measurements of concentration and temperatures within the release plume were made. Flow rates for the larger releases were estimated by calculation.
After all ov these experiments, DNV GL carried out a review with the purpose of assessing the robustness of the data recorded. As part of the data review a method was derived to estimate the time-varying flow rate analytically from derived pressure and temperature measurements in the reservoir.
The data review concluded that while the data will be extremely valuable for model validation, the measurements for the large-scale diameter experiments is not as high quality as that from previous smaller-scale diameter tests carried out by BP and Shell.
This was due to difficulties achieving accurate measurements at the larger scale. To assist in the data review, DNV GL Phast discharge models were used to provide a reference source. The experimental data and results of the data review have been made public by CO2PIPETRANS JIP. This data provides valuable validation material to the CO2 dispersion modeling community.
Fracture Arrest
Fracture propagation is the phenomenon of a pipeline rupture growing beyond the length of the initial rupture in the pipeline due to the force of the expanding fluid exiting the pipeline. For CO2 pipelines this phenomenon is not well understood and is complicated by the phase difference between typical operating conditions of a CO2 pipeline in liquid phase and atmospheric conditions where CO2 exists as a gas. This phase change provides an increased driving force for fracture propagation compared to natural gas pipelines.
The objective of this part of the joint industry project is to investigate the validity of using methods from natural gas pipelines to estimate the material and wall thickness requirements to resist fracture propagation. The Battelle Two Curve method is a commonly used approach for expressing the variation of crack velocity and gas decompression velocity with pressure. CO2PIPETRANS Phase 2 aims to validate this method with a program of experimental testing.
The experimental program involves two sets of experiments, starting at a smaller scale, and then building to full-scale burst test experiments. The first experimental program was undertaken at Giskås in Norway in 2012 to show arrest and propagation as predicted with the Battelle Two Curve method on 16-inch pipe.
The experimental set-up was designed to measure both the speed of the fracture running through the pipeline material and the speed of the decompression wave of the CO2. The speed of the fracture is measured with timing wires around the outside of the pipe that are cut as the fracture passes. The decompression wave is measured with high-speed pressure transducers inside the pipeline.
The tests were initiated with an explosive charge that accurately cut the pipe material in the center of the test section. The pipe material and wall thickness were kept constant in both tests – four pipe joints with varying wall thickness or material strength for each test, and the saturation pressure of the CO2 adjusted by controlling the fluid temperature to achieve fracture arrest or propagation.
The design of the test program at Giskås in terms of pipe size, material strength and test conditions, was established through close cooperation within the technical advisory group of the JIP with all partners represented.
The second experimental program is a collaborative approach, funded by the European Commission, The European Pipeline Research Group and CO2PIPETRANS. It is known as the Requirements for Safe and Reliable CO2 Transport Pipelines (SARCO2B) program. The experiments are being conducted in Italy with full-scale, 24-inch (0.6m) in diameter test sections. In this set of tests, the setup is similar to the first, but the saturation pressure of the CO2 is controlled by altering the composition of the fluid.
When the results of the experimental programs are combined, it is hoped the existing models will be validated or a new methodology suggested. This will ensure the risks of fracture arrest are adequately addressed during design and reflected in design codes such as DNV-RP-J202.
Corrosion
Typically, internal corrosion control philosophies for CO2 carrying pipelines are based on controlling water content and impurities. These prevent the formation of free water and hence carbonic acid inside the pipeline. The challenge is to understand what combination of water and impurities can cause unacceptable corrosion rates.
The objective of this work package was to determine the mechanism and corrosion rate in dense phase CO2 for various impurities resulting from CCUS applications, including O2, SOx, NOx, and H2S with and without free water.
The experimental work was carried out using a specialized rotating autoclave for performing CO2 corrosion experiments, which provides good mixing and disturbed flow around the test specimen. The test specimens used in the setup were selected grades of carbon steel and stainless steel, typically used as pipeline materials.
The experiments were carried out at two temperatures; 39° F (4° C) and 122° F (50° C), at a pressure of about 1,450 psi (100 barg). Different combinations and concentrations of the impurities O2, SO2, H2S, NO, NO2 were added to the pure CO2 with water concentrations of 50 and 500 ppmv. Published quality recommendations from the European Union-funded CO2 research project called DYNAMIS were used as a starting point to decide the concentrations of the impurities to be tested. After the corrosion testing, the metal loss was determined, and the corrosion rates were calculated.
Based on these results, an update of DNV GL’s recommended practice for design and operation of CO2 pipelines (DNV–RP-J202) will be made. This will describe how to define a safe operating window for dense phase CO2 containing various impurities. The results do not eliminate all of the uncertainty, but is a step in the refinement of the operational limits for different impurities found in pipelines carrying anthropogenic CO2 and the moisture content.
What Next?
Data is now publicly available to validate CO2 dispersion models and additional data is due to be released in early 2015. With the completion of the full-scale fracture arrest experiments in early 2015, the last phase of CO2PIPETRANS will also be completed.
The CO2PIPETRANS project has increased the understanding of the impurities that can affect the corrosion rates in CO2 pipelines and has shown that controlling water is a satisfactory measure for controlling corrosion. However, further work is required to refine the understanding of these limits and mechanisms.
The jury is still out on the applicability of the Battelle Two Curve method for predicting fracture arrest in CO2 pipelines. It is hoped that further experimental work will help to narrow the gap in our current understanding in order to build safe pipelines without expensive overdesign.
Authors: Jock Brown is project manager for the CO2PIPETRANS JIP and a senior consultant in carbon capture, utilization and storage with DNV GL, based in Oslo, Norway. He holds a master’s degree in chemical engineering from Canterbury University in New Zealand.
Authors: Tom Bubenik is a senior principal engineer with DNV GL, based in Columbus, OH and is an expert on running ductile fractures. He holds a doctorate in theoretical and applied mechanics from the Northwestern University.
Brit Graver is a senior engineer in materials technology with DNV GL, based in Oslo, and technical expert for the corrosion work package in CO2PIPETRANS. Graver holds a doctorate in materials science and corrosion from NTNU in Norway. Kaare Helle is a principal consultant in carbon capture and storage with DNV GL, based in Oslo, and is the project responsible for CO2PIPETRANS. He holds a master’s degree in mechanical engineering from NTNU. Hamish Holt is the CO2PIPETRANS JIP work package manager for delivery of the CO2 release experiments at Spadeadam. He is a principal consultant with DNV GL in Aberdeen, UK, and holds a master’s degree in mechanical engineering from Herriot-Watt University in the United Kingdom. Sigbjørn Røneid is a senior pipeline engineer at DNV GL, based in Oslo, and leads the fracture arrest work package testing in Norway and Italy. He holds a master’s degree in naval architecture and marine engineering from NTNU.
Comments