June 2014, Vol. 241, No. 6
Features
Helping Operators Comply With New IVP Regulations
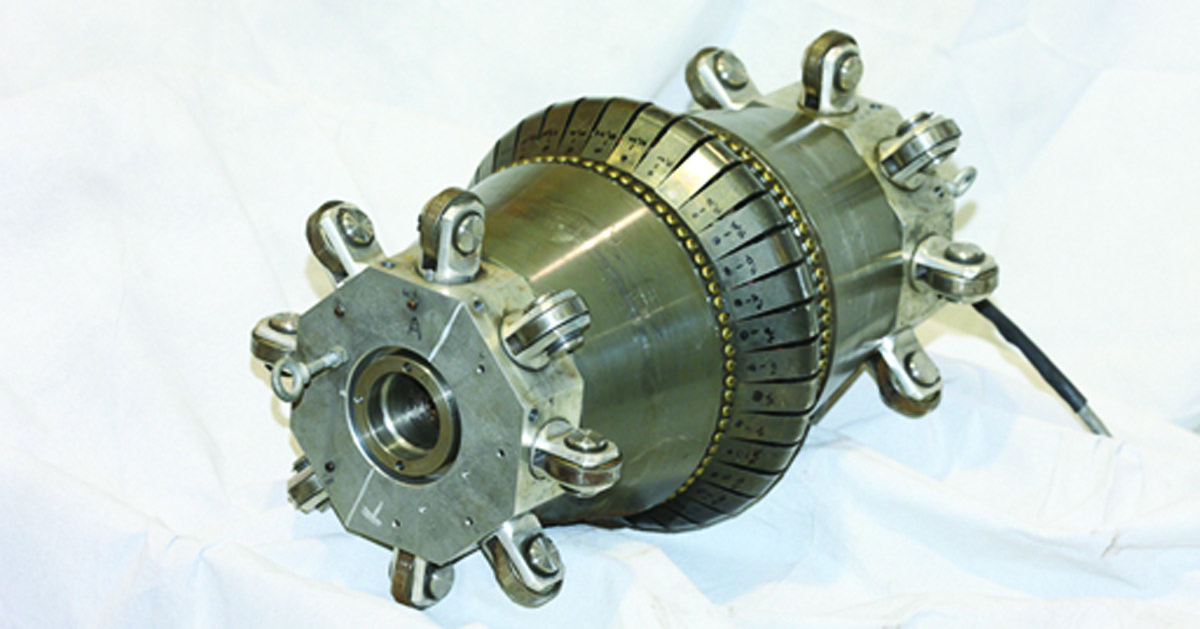
Last summer the Pipeline and Hazardous Materials Safety Administration (PHMSA) previewed proposed additions to its integrity management program (IMP) which require operators to test pipe segments located in high-consequence areas (HCAs) and to “devote additional focus, efforts, and analysis … to ensure the integrity of [those] pipelines.”
These additions will result in what are known as integrity verification process (IVP) regulations. As it stands, these requirements would require pipeline operators to verify maximum allowable operating pressure (MAOP) and material properties of gas transmission lines, including pipelines constructed before 1970 that had been grandfathered from testing protocols.
It is estimated that the new regulations could cover 91,000 miles of gas transmission pipelines, including those in HCAs, as well as regions that could be classified as moderate consequence areas (MCAs) not previously included in the IMP.
New Tools For IVP Compliance
Conforming to pending IVP regulations using currently allowed techniques presents a host of operational challenges and cost implications for the natural gas industry. The new regulations may require operators to perform material testing for transmission pipe that does not have validated and traceable material property records.
Researchers at Gas Technology Institute (GTI), a global research, development, and training organization, with support from Operations Technology Development (OTD), a partnership of natural gas distribution companies formed to develop new gas operations and infrastructure technologies, are working to develop cost-effective solutions for IVP compliance.
Techniques For Property Verification
In the past, a pipeline with unknown yield strength was assigned a conservative value of 24,000 psi. Based on that assumption, many pipelines were calculated to operate at over 20% specified minimum yield strength (SMYS) when they were actually operating below 20% SMYS. Until recently, operators had only one alternative to accepting that inaccurate assumption — destructive testing. Because of the large sample sizes required by the API 5L specification, that testing required either a line shutdown or a bypass system.
GTI researchers are aiming to change that. In a test program conducted on over 40 real-world pipe samples, a team demonstrated it is possible to determine yield strength without interrupting service by simply removing 6-inch hot-tap coupons from a pipeline and sending them for lab testing.
Smaller full-wall specimens from a hot-tap coupon were tested and compared with full-sized samples and found to be superior to the full-sized samples in several respects. They were always conservative, more robust, simple and more repeatable. And, of course, less intrusive.
In addition to a new testing technique, researchers developed and validated an alternative sampling methodology with the potential to provide superior confidence compared with the prescriptive sampling interval now required by integrity management regulations (49 CFR, Part 192). The new technique uses adaptive sampling that updates the required numbers of samples based on results.
“Using this method, operators will be able to classify pipeline segment properties with a known confidence level and to determine the likelihood of a weakest link section,” said Daniel Ersoy, GTI Research and Development executive director. “If the data and code allow, operators may be able to reduce the overall number of samples required to verify the material properties of a line segment.”
The new alternative yield strength-testing technique has already received acceptance and approval for use by PHMSA and Oregon’s state regulator through the special permit process.
New Correlation Factors
Going forward, the GTI team will continue to investigate ways to use non-destructive material property testing, including stress-strain microbes and other surface measurement techniques.
To overcome one potential barrier to this approach – the need to account for variations in material properties through the wall thickness – the company has launched a new research program. The goal is to quantify this potential variability to allow these surface measurements to be used with the appropriate safety factors, based on vintage and other relevant characteristics.
Pressure Testing Alternative
Pending IVP regulations could require operators to hydrotest those pipelines in an HCA that did not have a post-construction hydrotest and are operating above 20% SMYS. However, because hydrotesting introduces water to the pipeline that cannot always be fully removed – potentially leading to accelerated crack growth in some pipeline materials – stakeholders are seeking alternatives that might provide an equivalent assessment.
Researchers are attempting to validate that ILI tools can, in some situations, provide an assessment that would find any defect that would fail a hydrotest. Partnering with Quest Integrated (Qi2), an integrity management company, GTI is creating critical flaw curves for various pipe configurations (yield strength, diameter, wall thickness and SMYS percentage).
The critical flaw curves will range from smooth metal loss flaws all the way to sharp planar cracks. The end result of the research will be a calculator that operators can use to determine the performance requirements of ILI tools for a specific line segment to provide a hydrotest equivalency.
Documenting Properties Of Fittings
Because of the broad scope of the proposed IVP regulations, operators may be facing the challenge of providing “validated, traceable materials documentation” for thousands of fittings. In cases in which operators do not have “mill-equivalent” or design and material documentation for their fittings and components, it may be necessary to cut them out or de-rate pipelines.
Researchers are working to provide operators with additional tools for identifying the material properties of fittings. A catalog of legacy fittings and components is being developed to help operators identify and characterize the material and mechanical properties of their assets.
The catalog will provide listings of vintage and legacy fittings, appurtenances, ells, tees and valves, as well as the material design and strength classes each was manufactured to, so that operators can, at a minimum, assign conservative assumptions about the fittings’ properties.
The catalog will contain available images, descriptions, strength class ratings, and material and mechanical properties for the selected fitting and components. In order to provide additional assistance with identification, the catalog will include information about the location of component markings and distinguishing features, such as flange thickness and bolting patterns.
In addition to gathering information from industry literature, the team is working with manufacturers and operators to collect supplemental information, including a breakout by manufacturer year or vintage, if possible.
When a fitting can be positively identified, the catalog will provide support for strength requirements and assumptions. The goal is to provide operators with a way to reduce the cost of gathering and compiling information needed to comply with IVP requirements.
What About Unpiggable Pipes?
Many local distribution companies (LDCs) operate pipe segments classified as transmission and potentially subject to pending IVP regulations. Yet, a large portion of these segments is classified as unpiggable, or difficult to inspect with conventional inline inspection (ILI) tools that were designed for use on high-pressure transmission lines.
Researchers are investigating technologies that can help operators reduce their exposure to integrity threats and unknown pipe defects when inspecting segments of unpiggable pipe.
Leveraging magnetic flux leakage (MFL) technology, researchers have been working with industry partners to enable the application of MFL technology for live inspection of short unpiggable pipeline segments using a modified and patented MFL technology.
Pipecrawler, an inspection platform for unpiggable pipe comprises a tethered inspection platform that uses brush-drive units powered by electric linear-drive motors for propulsion. The current version, which features MFL sensors, has the ability to inspect up to 3,000 feet of pipe in pressures, up to 700 psi and to access a pipeline from a single location.
Electromagnetic acoustic transducer (EMAT) is a promising technology that offers the ability to detect and characterize corrosion, stress corrosion cracking (SCC), cracks, mechanical damage, laminations, coating disbondment and lack-of-fusion that can be used in live natural gas pipelines without a liquid couplant.
It is an ultrasonic transducer (UT) sensor that uses alternating current in a wire to induce an eddy current that can identify and characterize many defects – planar or tight-fitting cracks, in particular – that traditional MFL cannot. Recent advances in the technology have enhanced performance, including improved probability of detection (POD) and probability of identification (POI) for anomalies.
Comments