September 2011, Vol. 238 No. 9
Features
Recent Developments In Testing Wet Gas Flow Meters
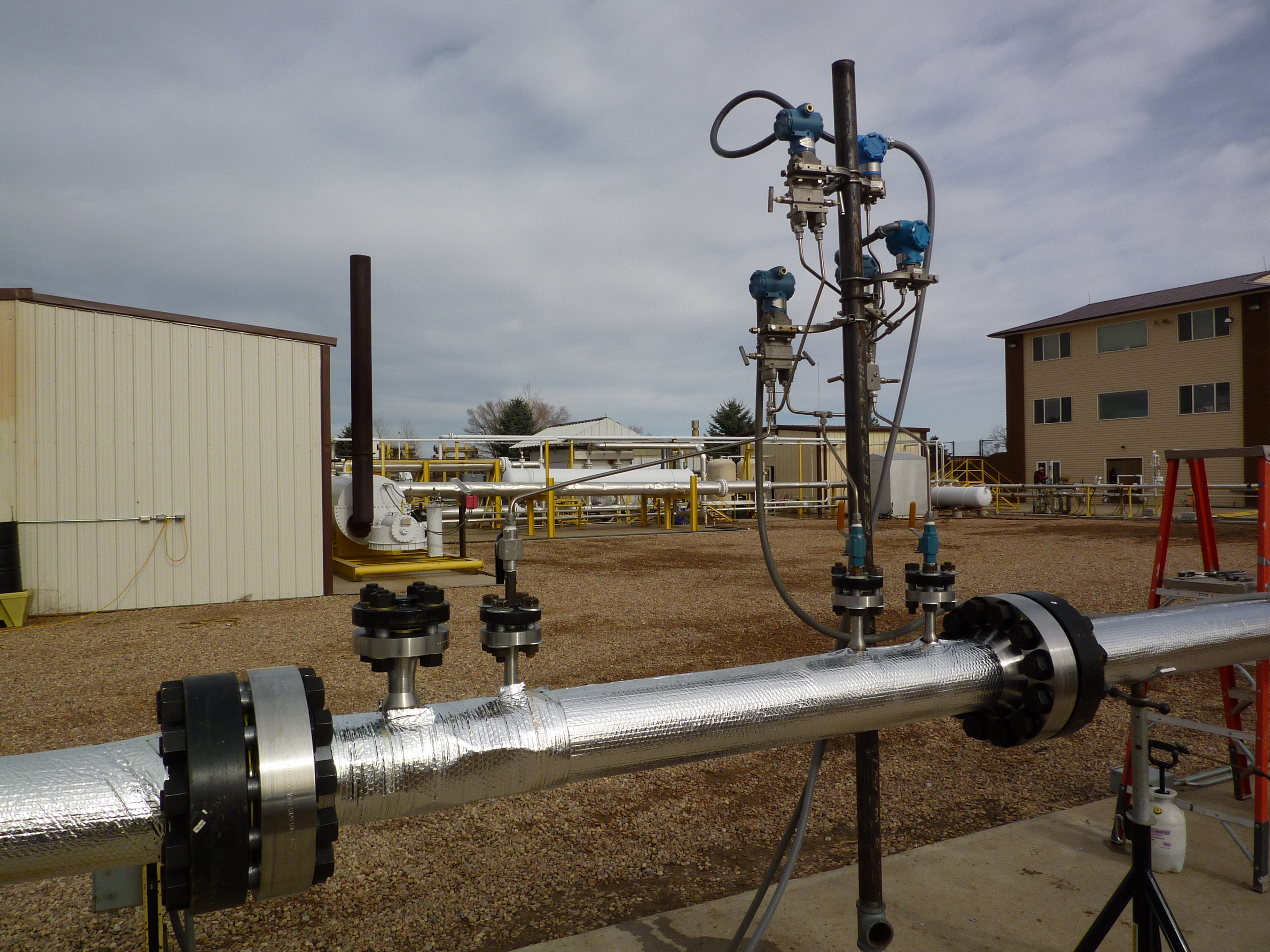
Natural gas is being produced from many varied and challenging locations around the world. Gas-prone reservoirs tend not to produce clean dry gas flows but rather wet natural gas flows where the gas is mixed with hydrocarbon liquids and water. Furthermore the wet natural gas production from each reservoir is unique. No two wet natural gas production flows are identical.
During 2006, in an interview conducted by Colorado Engineering Experiment Station Inc. (CEESI), Hans van Maanen of Shell Exploration & Production stated with a smile, “Show me any set of wet gas flow conditions and I will find such a well somewhere in the world.”
The technical challenge of metering this huge range of wet natural gas flow conditions is considerable. Significant continuous research and development on the metering of wet gas flow (i.e. flow predominately of gas by volume with some entrained liquid flow) has been ongoing for more than a decade. Today, the benefits of these efforts are evident in the world of hydrocarbon production. Whereas there were a very few rudimentary wet gas meter technologies available in the 1990s (other than the default of a separator with outlet single phase flow meters) there is now a choice of wet gas meter technologies available to the end user, all with pros and cons.
Figure 1: There is no a choice of wet gas meter technologies, each with its pros and cons.
Such is today’s availability of wet gas flow meters, and the hydrocarbon production industry’s potential use for them, that – in 2007 – Bob Webb of BP produced a “wish list” of locations where it would be beneficial to apply such technology. A Webb diagram is included for wet gas flow producing wells. Each individual well is seen to have a wet gas meter at the wellhead, to tell the operator individual well flow information. However, individual well flows are comingled in a flow line upstream of a communal separator.
The commingled wet gas flows in the flow line are ideally also metered by a wet gas meter. Separators are designed to split two-phase flow (i.e. flows of gas and liquid) into single phase flows but it is widely recognized that it is a common occurrence in the field for separators to operate at less than 100% efficiency. This means that the outlet pipe line designed for single phase gas flow can operate with wet gas flow and the outlet pipe line – designed for single phase liquid flow – can operate with multiphase flow. Hence, wet gas and multiphase flow meters may be preferred in these respective locations.
Only after processing is the requirement for multiphase and wet gas flow meters seen to pass. Therefore, the oil and gas industry has plenty of reason to desire reliable, accurate and affordable wet gas flow meters. However, few would claim that wet gas meter technology is mature. Developments and improvements continue at a steady pace. Such is the difficulty facing the oil and gas industry. There is a huge range of wet natural gas flow conditions across the world requiring accurate flow measurement and there is a limited range of maturing technologies developed and tested over limited wet gas flow conditions to apply to the task.
Figure 2: The task of developing a successful wet gas flow meter is made more difficult by the varied uses required of the meter.
The task of developing a successful wet gas flow meter is made more difficult still by the varied uses required of the meters. If the task of successfully developing wet gas meter technologies to cover the huge range of production conditions was not daunting enough, the task became yet more difficult when the required abilities of wet gas flow meters depend on individual applications. That is, the oil and gas industry requires wet gas flow meters to achieve many different objectives.
These range from measuring the gas flow alone (and ignoring the liquid flow), measuring the liquid flow only (and ignoring the gas flow), metering the individual gas, water and hydrocarbon liquid phase flow rates, to solely monitoring even trace water content of a wet natural gas flow (with a mixture of gas, water and hydrocarbon liquids) for flow assurance purposes.
The monitoring of trace water content can in fact be all important, as water can pose a threat to flow assurance. Water can causes the development of hydrates and the depositing of scale, salts and wax in the pipeline. Monitoring the water content of a wet gas flow therefore allows the operator to take the appropriate flow assurance actions.
Wet gas flow meters are used to estimate production rates from reservoirs. This information is not only useful for allocating production share and any fiscal responsibilities but often, just as importantly, for allowing reservoir engineers to estimate and control well production rates to maximize the return from that asset. Hence, even with the significant challenges of developing wet gas flow meters, the considerable importance of wet gas meter technology to the oil and gas industry has driven their development on for over a decade.
However, the development of these wet natural gas flow meter technologies has largely depended upon the existence of a few industrial-scale wet natural gas flow test facilities.
It is known that the response of wet gas meter technologies is directly linked to many different parameters. These include the size of the pipe line, the type of liquids flowing with the gas, the line pressure, the gas velocity, the relative amount of liquid to gas, and orientation of the meter. The outcome of this complexity is that no wet gas flow meter technology can meter a wet gas flow using theoretical considerations alone.
All wet gas meter technology relies to some extent on empirical or semi-empirical data, i.e. data originating from field tests and/or one or more of the world’s wet gas test facilities. However, whereas wet natural gas flow meter field data has its place in R&D projects it can not replace the service of the wet gas flow test facilities. Although field data is from the real live production flow, it has two distinct limitations. The first is that when installed in the field the meter cannot typically be tested over a wide range of conditions. The researchers are limited to whatever flow conditions that particular reservoir is producing.
The second is that the field gas and liquid phase production flow rates are typically not known to the required low uncertainties for wet gas meter R&D projects. Hence, whereas field tests are necessary for final testing, the R&D on wet gas meter technology requires the controlled varied wet gas flow conditions and low phase flow rate references of wet gas flow test facilities.
The demand for industrial scale wet natural gas flow test facilities is usually from three types of projects. Wet gas flow test facilities are necessary to carry out Factory Acceptance Tests (FATs) where the end user checks the claimed specifications of a manufacturer’s meter against known wet gas flow reference conditions. They are also required to characterize a wet gas meter by finding correction constants for the meter software. Wet gas flow test facilities are also indispensible for R&D of wet gas meter technology. However, despite the industry’s need industrial wet natural gas flow test facilities are expensive, complex and rare.
Each wet gas flow test facility is unique and each has different pros and cons. Each has its own range of test conditions. Due to the huge range of wet natural gas flow conditions that exist throughout industry, no wet gas flow test facility can cover all desired test flow conditions. Often then, the researchers are left with the requirement to extrapolate data on at least one and usually more parameters.
As such, the few industrial-scale wet gas flow facilities do not tend to be rivals. In reality, they complement each other with their different wet gas flow condition ranges expanding the over all testable wet gas flow condition range available to the operators and the meter manufacturers. Most serious wet gas flow metering researcher projects use all the test facilities.
CEESI has more than a decade of experience of testing wet gas flow equipment for the oil and gas industry. Originally built in the late 1990s by demand of a Joint Industry Project (JIP) that consisted of multiple oil and energy companies the CEESI wet gas test loop has been in continuous demand since its commissioning. However, wet natural gas flow test facility technology and capability has been required to develop and improve in pace with the technologies it is to test.
Keeping pace with the wet natural gas flow meter technological advances and the corresponding testing requirements has led CEESI to undertake two major expansions in the last four years. The original CEESI wet gas flow test facility was a nominal 4-inch pipeline with natural gas and hydrocarbon liquid as the flowing fluids. Much of the early test work in the early 2000s consisted of the oil and gas industry’s investigations into the response of various gas flow meter technologies to wet gas flow.
The general aim tended to be to understand the effect of the liquid on gas meter performance, and perhaps to quantify the effect for known liquid loadings. Such tests are still common today. Figure 3 shows a 2010 wet gas test at CEESI of a 4-inch Venturi meter. The CEESI view port is seen upstream of the meter under test. Such pictures on the physical dispersion of the phases of a wet gas flow have since proven indispensable in understanding the meters’ responses to wet gas flow. As the wet gas flow conditions change, the dispersion of the liquids in the gas change, thus changing the meter’s reaction to the liquid’s presence.
By the mid 2000s, the majority of the wet gas flow meter research had changed to the development and performance verification testing of wet gas flow meters capable of directly metering the gas and liquid flow rates without any external information regarding either one of the phases in order to predict the other phase flow rate.
During this period, the demand for the liquid phase to match the typical field production conditions with hydrocarbon liquid and water increased. That is, wet gas flow meter technology was developing to the point that various meter designs were being promoted as viable oil and gas industry products, and the real flow conditions were required to test and prove the meter concepts.
Figure 4: By 2007, the CEESI wet gas facility had been upgraded to a 4-inch “multiphase” wet gas flow testing facility.
By 2007 the CEESI wet gas facility was upgraded to a 4-inch “multiphase” wet gas flow test facility, i.e. a system capable of running natural gas with hydrocarbon liquid and/or water. The specifications of this 4-inch facility were pressures between 15 and 75 bar (abs), temperatures held nominally at ambient, gas flow rates up to 650 m3/hr, water flow rates up to 14 m3/hr and hydrocarbon liquids up to 14 m3/hr. The CEESI view port recorded multiphase wet gas flows at flow conditions never viewed before.
Figure 5: The CEESI view port has recorded multiphase wet gas flows at flow conditions never viewed before. A) 4-inch gas/water stratified flow. B) 4-inch gas/water/hydrocarbon liquid mist flow.
From the commissioning of the CEESI multiphase wet gas flow meter in 2007, the system was overbooked. One of the major client groups was the multiphase flow meter manufacturers. Multiphase flow meters are defined as meters that read the individual gas, water and hydrocarbon liquid flow rates of a multiphase flow, including multiphase wet gas flows, i.e. wet gas flows where the liquid phase is split between water and hydrocarbon liquid phase. A primary purpose for these tests was FATs as operators attempted to judge the true uncertainties of the new complex metering systems.
One of the most important abilities any wet gas flow test facility can have is flexibility. Wet natural gas flow meter test installations are usually very specific to the meter type under test and the installation for which it is to be used. That is, a primary requirement of a wet gas flow test facility is the ability to correctly mimic the assortment of installations that wet gas meters will be used in throughout industry. As such, the arrival of the multiphase flow meters significantly increased the vertical up (and occasionally down) wet gas flow testing at CEESI.
Figure 6: Multiphase meter installation mock up at CEESI.
Largely driven by the industry demand for testing large (i.e. ? 6-inch) multiphase wet gas meters, CEESI has just completed the second upgrade in less than four years. The CEESI multiphase wet gas flow test facility is now rated as capable of testing up to a nominally 8-inch wet gas flow metering system.
Such is the oil and gas industry’s current demand for wet gas flow test facilities and the significant strain on supply, while some pushed CEESI for the upgrade to accommodate larger meters and not to delay, others pushed to delay such an upgrade to extend the test slots available for 2011. In the end the significant upgrade took place in three months during summer 2011 with the deadline for the first set of 8-inch meter tests set from the outset of the project.
The specifications of this 8-inch facility were pressures between 15 and 75 bar (abs), temperatures held nominally at ambient, gas flow rates up to 1,870 m3/hr, water flow rates up to 28 m3/hr and hydrocarbon liquids up to 28 m3/hr. Again, the unique CEESI view port design recorded multiphase wet gas flows at flow conditions never viewed before.
The first 8-inch multiphase wet gas meter tests were under way as this article went to print. Today, there are only two wet gas flow meter test facilities in the world capable of testing multiphase wet gas flow meters with natural gas, water and hydrocarbon liquids at realistic flow rates and pressures. These are CEESI and K-Lab. As stated earlier, there is no great rivalry between CEESI and K-Lab.
Such is the demand that CEESI predicts that the K-Lab back log – typically in excess of a year – will not be eased by the commissioning of the CEESI 8-inch, but rather CEESI may join K-Lab in having orders for testing stretching for many months. What is sure however, is that the arrival of the CEESI 8-inch multiphase wet gas flow test loop on the market should go a long way to helping alleviate the significant mismatch that exists between supply and demand for multiphase wet gas flow testing.
Authors
Richard Steven has been the director of the CEESI multiphase wet gas flow test facility for six years. With a Ph.D. degree in mechanical engineering (specializing in experimental fluid mechanics) his work experience includes as an independent researcher at TUVNEL in the UK and as a meter designer with McCrometer in the U.S. He is the chairman of both the ASME and ISO TC193 committees on wet gas flow metering. Contact: 970-214-5614, rsteven@ceesi.com.
Joshua Kinney has worked as a technician at CEESI for 20 years and has been the manager of the CEESI wet gas flow facility since its commissioning in 1998. In the last 12 years, he has installed and tested the majority of wet gas flow meter systems in use in the industry as developing prototypes and / or commercial systems under customer acceptance testing.
Charlie Britton is a mechanical engineer who has been involved with CEESI since the company was founded. As the designer of the main CEESI flow test facilities he has deep experience in flow meter test laboratory design. He was the designer of the original state-of-the-art CEESI wet gas flow facility and the designer of all the CEESI wet gas flow upgrades since.
Comments