July 2009 Vol. 236 No. 7
Features
Video Technology Developed In The Water Industry Can Monitor Pipeline Facilities
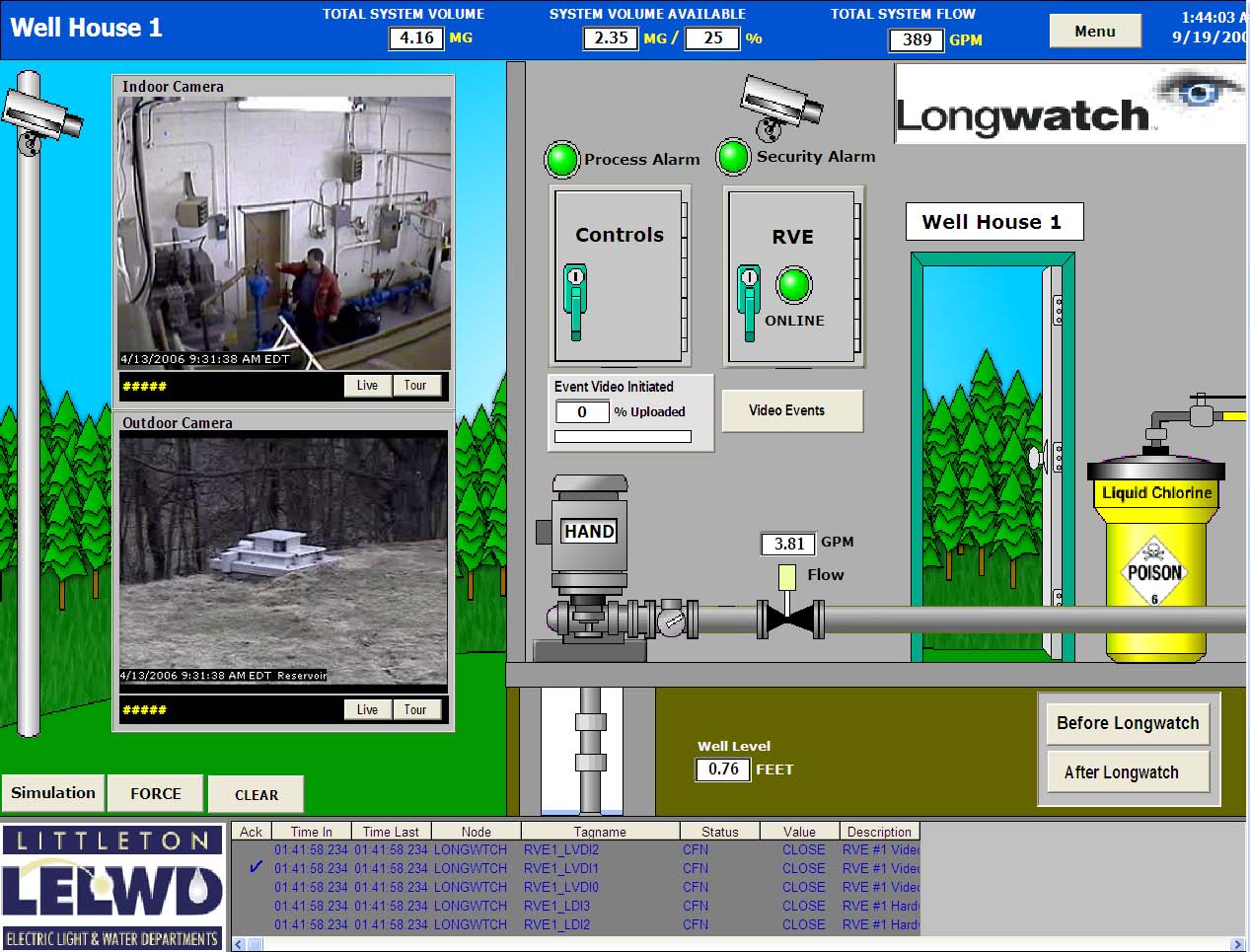
In the pipeline industry, real-time monitoring is becoming a big business. Systems monitor pipeline integrity, temperature, vibration, leaks, personnel and equipment, as well as watch for intruders. These systems use a variety of communication methods, including fiber optic cable strung along the pipeline, cellular, satellite, wireless and Ethernet.
Advances in video monitoring in the water and wastewater industries can be applied to pipeline applications. Water plants in the U.S. have installed video monitoring equipment to watch over their fences, entry points, remote facilities, lagoons and properties, Figure 1. In many cases, they connected the security video to their HMI/SCADA systems using industrial networks, wireless and cellular network connections. The main reason for connecting to existing networks was that it was far less expensive than to install dedicated CCTV or broadband cable.
Figure 1: Water treatment plants pioneered the use of video in HMI/SCADA systems. Here, a water plant in the U.S. displays video clips transmitted over the plant’s industrial network on a Wonderware HMI system.
The same technology applies to pipeline monitoring, making it possible to install video cameras anywhere along a pipeline, from offshore platforms and wellheads to compressor stations, LNG plants, and distribution points. By using existing communications capabilities and bringing video directly to HMI/SCADA screens, operators can see what is happening at remote facilities, diagnose problems, and minimize the need for personnel site visits. The challenge in any of these systems includes the following:
- Making sure that the video transmissions do not interfere with monitoring and control signals and
- Integrating video into the SCADA/HMI system so the operator can easily relate process alarms and video information.
Adding video monitoring to existing networks and HMI/SCADA systems is a well-developed technology. Longwatch pioneered the use of industrial networks for connecting video to Wonderware, Rockwell, GE Fanuc iFix and other HMI/SCADA systems. Consequently, it has dozens of installations across the U.S. in water plants. Emerson and Invensys also offer video security monitoring systems connected to HMI/SCADA. Simply dropping a video window onto an HMI/SCADA screen is now a common practice.
Video For HMI/SCADA Systems
Traditional video monitoring in a gas processing plant involves remote analog cameras connected via CCTV coaxial cables to a bank of monitors in a guard shack. Not only is this an expensive solution, it requires eternal vigilance by security personnel to make sure they don’t miss anything. If conventional video monitors are installed in a control room, they take up valuable panel space, and also require constant observation.
A modern digital camera system improves on this installation in four ways: First, it allows multiple cameras to be connected to a single cable or wireless connection; second, it uses an existing industrial network to transmit the images, thus eliminating the need to run additional cable; third, it puts the video images directly onto an HMI/SCADA screen, so operators can monitor what is happening in a process unit; and fourth, modern digital cameras and video processing software can identify intruders and anomalies in the image, and alert the operator by integrating video alarms into their existing SCADA/HMI system. Figure 2 illustrates how such a system works.
Figure 2: In the Longwatch video surveillance system, up to 12 cameras at a remote site connect to a local Video Engine, which acquires and stores their continuous high-resolution images for up to 30 days. The video engine transmits “video clips” when requested by the control system, a local alarm, or when it detects an intruder or anomaly in the image. Video clips are transmitted as Ethernet packets over the in-plant network, wireless system, or a cellular network to the Video Control Center in the control room. The Control Center stores the clips in a Video Historian and provides video images to an HMI, cellphone, Internet browser, and other systems on the network.
A modern camera system continuously records high-resolution video on a “Video Engine” for up to 30 days at the camera site (commonly called “recording at the edge.”) The system can be programmed to send live video to a SCADA/HMI system, or to take “video clips” at specific times of the day, when requested by the control system, or if local events occur, such as a process alarm, an intrusion, or if the camera itself detects an anomaly. For example, a digital camera can identify an errant crane hook passing in front of the lens on an offshore platform. The operator might have a different video image on the HMI, but the system can be configured so that it switches to the offshore camera, alerts the operator to the anomaly and shows the video.
Similarly, if a compressor station has an infrared camera or audio microphone that can detect gas leaks, the video engine will send a video clip to the operator. Once alerted, the operator can switch to live video to monitor the scene and direct a maintenance crew to the problem area.
The quality of the video depends upon the bandwidth available. On a high speed, gigabit Ethernet network or a high-bandwidth 3G cellphone connection, high resolution video can be transmitted. Conversely, on a low-speed radio network, short video clips may have to suffice. Longwatch video systems, for example, require a minimum of 9600 baud (1KB per second) bandwidth to transmit video images.
Typically, an analysis is made of the communication system to determine if enough bandwidth is available to accommodate video packets without interfering with higher priority messages, such as process monitoring or control signals. If so, the Longwatch video engine is configured to ensure that it does not use any more bandwidth than is permitted. Many pipeline communications systems are Ethernet-based, meaning that a video system can connect to virtually any existing system.
For Ethernet-based networks, the Longwatch video engine connects via an Ethernet port and has an individual IP address; similarly, the Longwatch Video Control Center computer in the control room has an IP address. Video images are sent in packets from the remote site, reassembled in the Video Control Center computer, and presented on the HMI screen. The Longwatch advantage in this configuration is that local video recording provides a level of fault tolerance (i.e., the video is preserved even if the network is unavailable.) In addition, the Longwatch system buffers the network messages so that bandwidth is preserved even during a flurry of plant or system events.
High-resolution video stored at the remote site can be retrieved at any time and either transmitted to the control room or loaded onto a thumb drive or portable recorder. Video clips are stored in a Video Historian on a PC in the control room. This combination of video storage allows operators and engineers to view any event or series of events.
Video Monitoring
Monitoring a pipeline control system has been described as hours of sheer boredom interrupted by moments of panic. Operators sit at HMI consoles, staring at bar graphs and animated representations of compressor stations, pipeline networks and wellheads. They are completely isolated from the process, and rely on their HMI screens to tell them what is happening. When an upset occurs, they have to figure out the problem remotely. If a valve is stuck, a pipe has burst, or if pressure is dropping, the HMI screen may not be able to give them enough information.
Video can. With video, an operator can call up a video image of the process in question, then pan, tilt and zoom the camera to see what is happening. The operator can even read local gauges and indicators. Once the problem is discovered, the operator can view video from seconds, minutes or days before the incident occurred to determine why it happened. Maybe someone hit the valve with a pickup truck three days ago. Perhaps an animal wandered into a wellhead and got caught in the equipment.
Even if a remote unit—such as a wellhead—is not connected to the plant’s SCADA system, cameras can be positioned to read local gauges and readouts, and transmit video via wireless or cellular networks. This lets operators check operations and conditions without visiting the site and thus save significant time and money.
Cellular data transfer offers an economical solution for remote process areas. For about US$60 per month, cellular data services provide a fast, bidirectional interface. Operators can pan, tilt and zoom remote cameras to read gauges or inspect the equipment, and watch high-resolution video live. Cellular coverage is increasing rapidly around the world, although it can be sparse in remote areas, such as Wyoming with its hundreds of gas wellheads. In that case, a radio system can be installed that has enough power to reach the central distribution location. Many wellheads are being equipped with solar or gas-powered generators to supply power for local controls and radio communications; the video system can piggyback on any of these power and communication systems.
If the remote site has no power or communications, a battery or solar system can power a Longwatch video system and cellular communication device. In such a case, the video system typically will power itself up, take a series of short video clips of the equipment and premises, transmit them to the control room, and shut down again. The system can power itself up on a scheduled basis, or in response to an alarm condition or a command from the control room. The battery can be replaced during normal visits by maintenance personnel.
For about US$10,000, a process unit can be equipped with 6 to 10 cameras, a video engine, local I/O to connect alarms and motion detectors, and a cellular, wireless or network interface.
Checking Instrumentation
Instrumentation is fairly reliable, but when it fails the operator may not know it. Also, instrumentation cannot detect everything. If a valve seal or pipe is leaking and it does not get detected by instrumentation, then visual inspection is the only possible detection method. If the instrumentation can cause a leak, by the time the problem is discovered, thousands of cubic feet of gas can be released.
At one power plant, operators could not understand why a tank was not unloading properly. The HMI screen said the pumps and valves were working, but the level in the receiving tank was not increasing. On-site inspection revealed that one of the pumping hoses had come loose, and the plant had pumped 1,500 gallons of fuel oil into the river instead of the tank. The plant has since installed a video monitoring system. The key benefit is that the video enables the operator to act quickly, avoiding the costs of clean up and EPA fines. It also provides more goodwill with their neighbors.
To check instrumentation and systems, one solution would be to perform a “test clip” at the beginning of each shift. This is the equivalent of “walking around the plant,” or visiting a remote site, because simply looking at a video clip makes it possible to see obvious faults in the process unit. The human eye is very good at spotting problems.
Even if the operators don’t look at the video clip, modern digital cameras and Longwatch comparative analytic software can spot anomalies in the image, such as escaping gas, a pool of liquid, intruders, and so on. Video might be able to spot a problem long before local sensors can sound an alarm.
Another key differentiator with video: Video will not show a switch to be in the off position when it is in the on position and it will not show that a door is open when it is closed, but it is possible for an instrument to give false readings in these cases.
Video Benefits
Many facilities function without operators today. Offshore platforms, wellheads, pipelines, compressor stations, and other facilities operate with only routine visits from maintenance personnel. The problem is: Not only are they unmanned, they are often unwatched. A cellular-equipped camera system can monitor just about anything, anywhere, 24 hours a day. With video, pipeline operators can:
- Eliminate or minimize periodic visits by maintenance personnel to remote sites. Video can read gauges, inspect for leaks, and diagnose problems, thus eliminating the need for personnel to make unnecessary trips.
- Identify problems. Being able to see a problem—and show it to maintenance people—ensures that the proper tools, parts and equipment are dispatched to the remote site. The crew knows whether to take a tool kit or a shotgun, for example.
- Provide expert service. If a maintenance crew comes across a problem that requires expert advice, video can be sent to a specialist thousands of miles away. The expert and crew can work together to solve the problem, using live video.
- Identify intruders. Video can detect intruders, alert an operator, and capture the intruder’s movements and actions on video that can be used for criminal prosecution.
- Observe personnel at remote sites when repairs or other services are being performed.
- Provide better emergency health care in case of an accident. Video allows medical personnel to see what happened, advise on-site workers, and dispatch the correct medical team.
The author– Steve Rubin is the president and CEO of Longwatch. He is an ISA fellow and founder and former CEO of Intellution, Inc., a pioneer in the HMI market. Longwatch Inc. is based in Norwood, MA. Phone: (781) 255-7400, (877) LONGWATCH, www.longwatch.com.
Comments