June 2016, Vol. 243, No. 6
Features
Columbia Pipeline Group Reaches 99% Availability
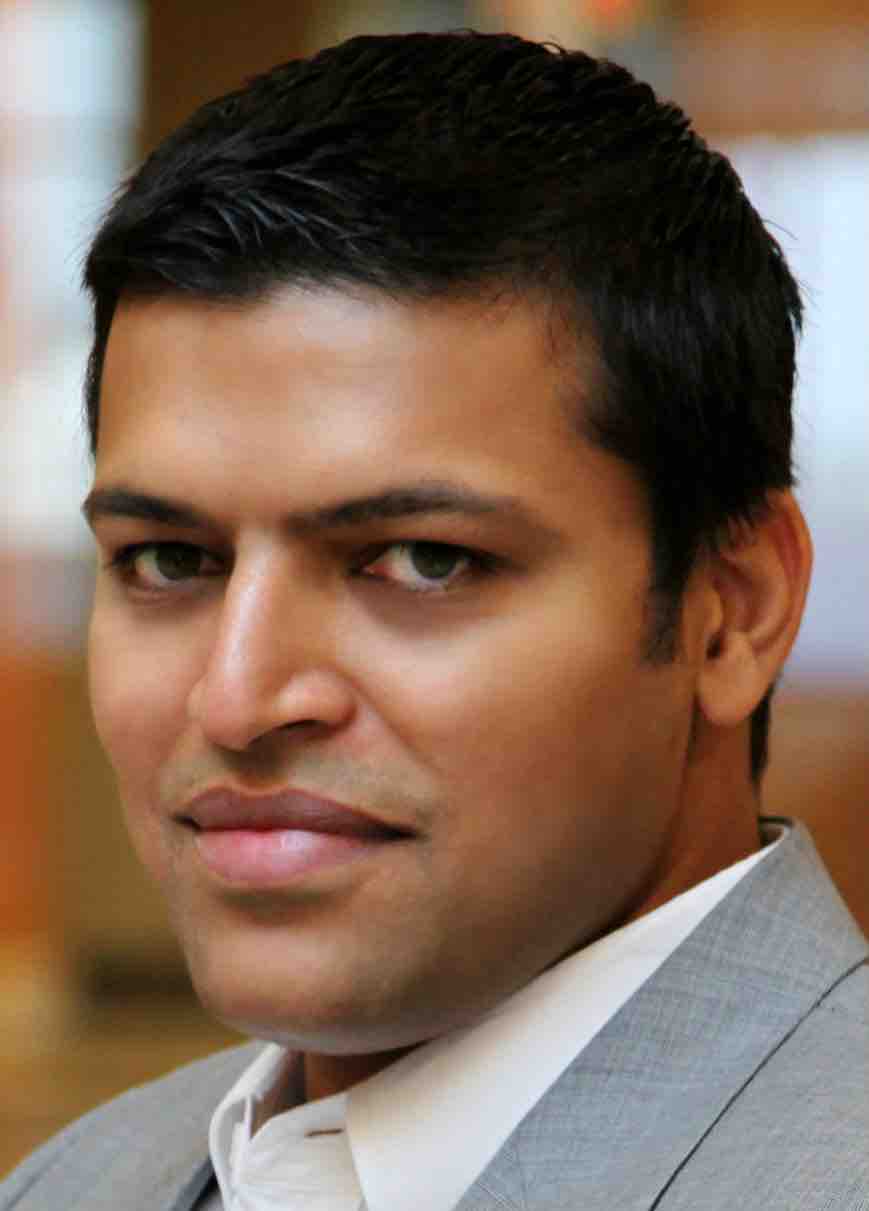
Changes to the oil and gas industry in the United States have put pressure on transmission companies to optimize their systems, add flexibility and respond more quickly to a fluctuating industry landscape. While many companies in the industry have been struggling to change, others have been more forward-thinking in applying new technologies.
Columbia Pipeline Group (CPG) improved its operational environment by implementing a modern distributed control system to improve reliability, gain better insight into its production data and ease maintenance. CPB saved about $2.3 million from reduced maintenance costs in one year, showing that gas transmission companies can reach over 99% reliability while running at 100% capacity.
Challenge
CPG runs nearly 15,000 miles of natural gas pipelines from the Gulf Coast to the Northeast, serving customers in 16 states. Before 2009, the transmission company left 20% capacity available in case of horsepower unit failures. When the company increased production to 100% capacity in 2009, it needed to gain reliability using other methods to ensure production wouldn’t come to a stop and negatively affect contractual obligations. The company had to either add more pipelines or increase the horsepower redundancy at its compressor stations.
The company also needed to gain better insight into production data and manage the long-term costs to more effectively maintain the system. The existing disparate and homegrown control systems had been increasingly difficult and costly to maintain. CPG used an in-house SCADA system that only one person knew how to support, and replacement parts were becoming difficult to find. Existing suppliers didn’t have good training programs for new maintenance staff, and current employees were retiring – taking their system expertise with them.
In addition, the existing systems didn’t provide the information management needed to proactively optimize operations or easily integrate with the corporate-level data warehouse. The lack of a secure user access and authentication system also put information security at risk.
Solution
The existing system wasn’t sustainable and the cost for adding additional pipeline was prohibitive. CPG management evaluated the company’s long-term needs and developed a five-year plan to modernize the control system across its pipelines. The team decided to standardize on one system across all of its pipelines to improve reliability through added redundancy, enable information sharing between stations and up to executive offices, and simplify long-term maintenance. CPG set a goal of reaching 100% reliability – at 100% capacity – by the end of the five years.
After a review of options, the CPG engineering team decided to standardize on a virtualized PlantPAx® process control system from Rockwell Automation. The high-availability, modern DCS would share more information across facilities and up to the executive level, enable remote access and improve security.
“We were planning to modernize our entire control system across 16 states and didn’t want to be managing multiple points of contact at the same time,” said Brian Sloan, automation and electrical engineering manager for CPG. “Working directly with one contact throughout the entire process has made a complex project easier to tackle.”
The CPG team installed redundant horsepower at strategic points across the footprint to meet the required pressure for reliable transmission. Programmable automation controllers (PACs) control engine functions. Operators manage individual engine operation via redundant human-machine interfaces, and all engine PACs connect to the main compressor station control panel.
Allen-Bradley® technology is used throughout the facilities. CENTERLINE® motor control centers (MCCs) with IntelliCENTER® technology support the auxiliary functions of the compressor station and engine units. The networked MCCs easily integrate with controllers in the existing system. Motor control components within the MCCs include PowerFlex® AC drives, SMC™ Flex soft starters, PowerMonitor™ 5000 energy monitors, and E3 Plus™ electronic overload relays.
When designing the process control system, the CPG team realized each station would require more servers than physically possible to handle all applications needed for security, data analytics and system management. The team decided to implement virtualized servers using the PlantPAx selection guide and best practices for adopting a virtualized automation system.
The Rockwell Automation team deployed high-availability, virtualized servers from its Encompass™ Product Partner, Stratus Technologies. The Stratus servers reduced the physical space of the hardware, eliminated the need to procure hardware for each new application, and reduced the likelihood of downtime due to hardware errors.
Each virtualized server runs multiple Rockwell Software® FactoryTalk® applications including Historian, View Machine Edition, View Site Edition, AssetCentre and ViewPoint software. ViewPoint software allows CPG operators to access the HMI applications from any location through a Web browser, enabling them to make real-time decisions about any issues that arise. Combined with historian software, the visualization capabilities of the system allow monitoring, reporting and data recording for immediate and future access. In addition, the historian platform tightly integrates with the corporate-level OSIsoft PI data warehouse system – further increasing operations data visibility and availability.
The information-enabled system runs on EtherNet/IP™, allowing data to flow easily from engines to the main control panel, the MCCs to the PACs, one compressor station to another, and stations up to executive offices. Allen-Bradley Stratix™ industrial Ethernet switches manage the secure, real-time information sharing.
The CPG engineering team implemented the AssetCentre software to help manage changes and control user access in the field. The CPG team set authentication parameters within the software to manage rights and capabilities each user is granted when using other FactoryTalk applications. The application also tracks and records user actions for increased security and future reference.
Because the system is information-enabled, the CPG Enterprise Analytics team can develop reports on station operations to improve predictive maintenance. When replacement parts are needed, the engineering team can easily purchase them off-the-shelf from local suppliers.
Results
By early 2015, the CPG team reached 99.5% reliability. Working with one point of contact at Rockwell Automation, it implemented the virtualized control system to 40 compressor stations and plan to roll out the redundancy upgrades to 52 more stations. The team can use the same system to design any new compressor stations, and expects the enterprise-wide system to run for at least 10 years before additional upgrades are needed.
With the system’s added redundancy, the company is able to meet contractual obligations and improve beyond that, making business changes based on specific data.
“We’re making more educated decisions based on real-time and historical operations data that we can access anywhere, including from our headquarters,” said Sloan. “We’ve been able to significantly improve company profitability as a result.”
Based on new insights into engine operations, the CPG engineering team conducts more active and ongoing preventive maintenance – and it’s yielding results quickly. The company saved about$2.3 million from reduced maintenance costs and downtime in 2014.
Comments